THE SECRET TO REPAIRING
All boats will need maintenance at some point in their life and some repairs such as scratches, cracks or small holes you may wish to fix/repair yourself or to get in one of the GRP Boat Repairs team to help you.
Preparing the area
Preparation is key to making sure you get a great finish, the starting point is to clean and clear the area of any chemicals or residues with acetone and making sure any loose material is chipped off and removed.
Shallow scratches and gel coat
The external gel-coat is the shiny, coloured resin where most of the light scratches occur. These are easy to fix with a light sand and then built back up with new gel coat. To order gel coat, contact your boat manufacturers with your model and serial numbers.
Older vessels may struggle to get a factory gel coat, so order a colour close as possible or mix your own.
Mixing gel coat is tricky so ensure you wear a mask, goggles and gloves. When you have your small amount of gel coat, add the hardener and add a thickening of chopped fibreglass for deeper gouges and scratches.
Bear in mind you only have 10 – 20 minutes once you have added the hardener, so do one scratch gouge at a time. Mix really well or it will be a sticky resin, that will take days to cure. Gelcoat as with resin is affected by humidity and temperature so make sure to do test patches before committing to the real thing.
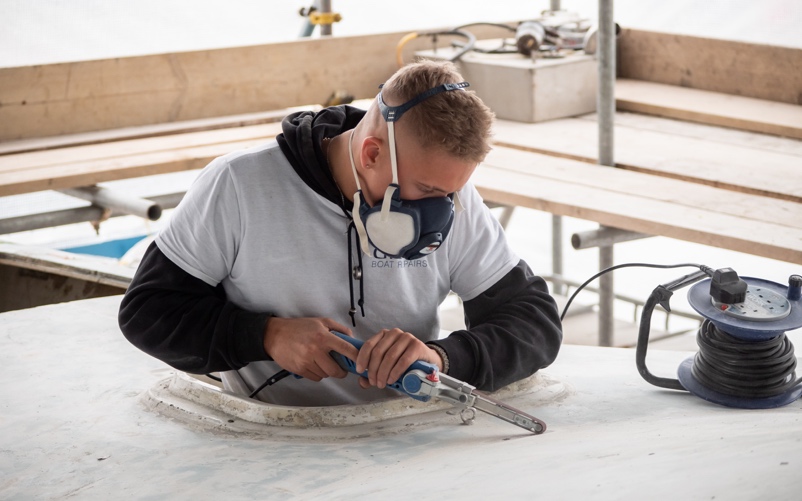
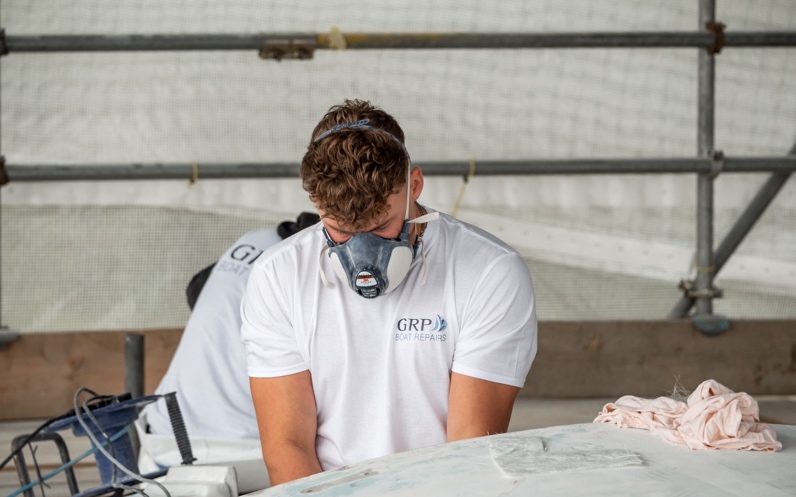
Holes and deeper gouges
Any hole which is to be repaired will need to be enlarged. Fibreglass boats have a thick structural core of fibreglass strands impregnated with polyester resin. If you can see these fibres then you know that the damage has gone deeper than the gelcoat.
Overfill gouges so the filler mounds slightly. You’ll sand it smooth after it cures. Curing can take between one and two hours dependant on temperature and humidity. You can test your repairs by touch, if it’s still sticky then it’s not fully cured. Once you’re fully satisfied that your repair has cured, you’ll then sand it level.
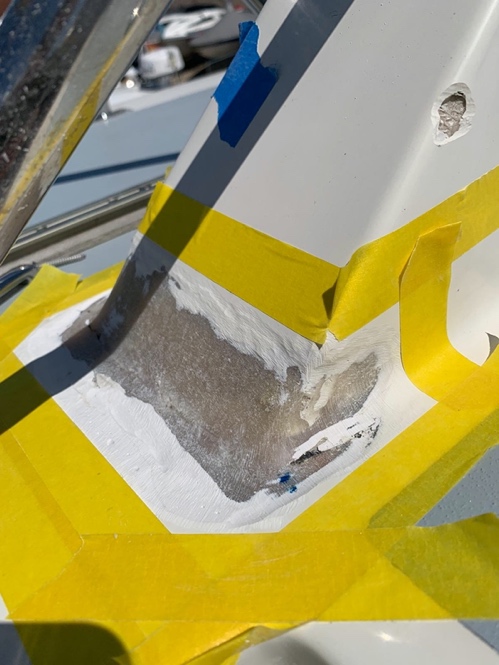
Any repair which is below the water line must have at least 7 days to cure enough before being immersed in water. Once dried the area will need to be sanded, starting with coarse and work up to 1000 grit. To finish the job, you’ll need a professional-type buffer.
Reinforcing Cloth and Fillers
The strength of a repair comes from the reinforcing cloth behind it, and there are three main types:
Pressed Chopped Strand Mat
Chopped strain mat has short strand fibres held together with a resin binder.
Woven Roving
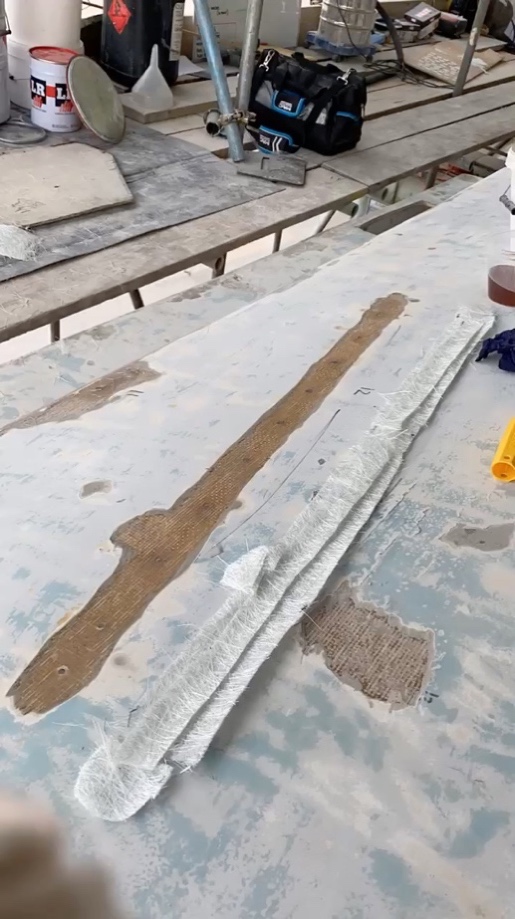
These are long strands of glass woven into a cloth that makes it strong and able to hinge without breaking up. It is ideal for use with all resins.
Stitched (engineered) cloth
Probably the best (and most expensive) material to work with, as it is particularly strong, and can be manipulated into very tight shapes.
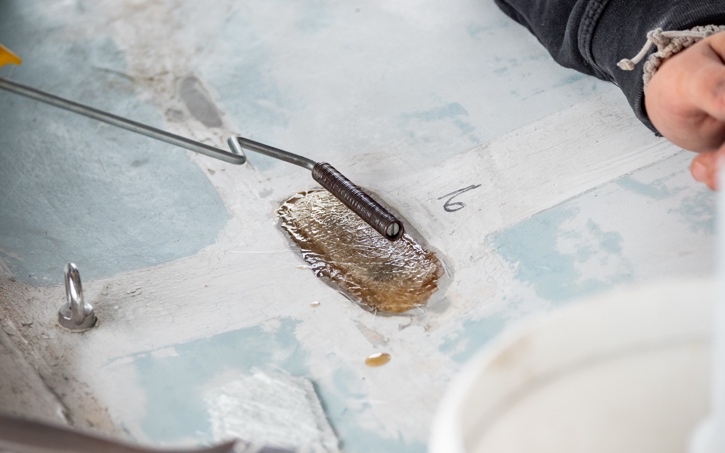
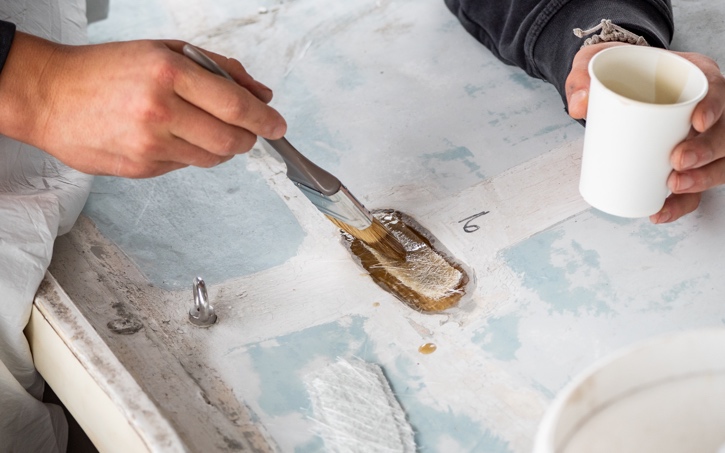
Resin
Polyester Resin
Most GRP production boats are made from polyester resin, a cheaper option than epoxy. It starts the curing process by simply mixing in a small amount of catalyst. But [polyester resin shrinks as it cures by as much as 4%, which can put strain on a repair,
Epoxy
Epoxy is probably more suited to repairs requiring bonding to other materials. There must be precise amounts with the hardener or the mix will be weaker. Epoxy is sensitive to temperatures and does not cure below 5°C, but if hot will harden fast.
How GRP Boat Repairs can help
At GRP we love fibreglass, it’s durable, strong and with a gel coat covering you will be giving your boat protection from the elements and resistance to scratches. If your repair job is too large to undertake on your own then get in touch with our team today and see if we can help.